Automation Upgrade for 5 GL Blow Molding System
Project Name
Automation Upgrade for 5 GL Blow Molding System
Industry Sector
Food & Beverage
Products & Services
- Schneider M340 PLC
- Schneider 7” GXU HMI
- Control Panel Designing
- Thermocouple Sensors.
Client Expectation :
The client sought to revamp the control system for their existing 5GL Blow Molding Machine, with the following key requirements:
- Removal of outdated PLC control panels, which were over 20 years old.
- Design and development of a new control system incorporating the latest technology.
- The project had a strict deadline of 20 days, with a maximum of 7 days allocated for shutdown.
Project Highlights
Temperature Control for Preform
Heating Chamber
Effective temperature control is vital for efficient preform heating. Our team perfectly tuned the Temperature control PID loops to achieve accurate temperature regulation.
Sanitary and Safety Guidelines
Our engineers adhered to all required sanitary and safety guidelines necessary for entry into the production facility of a food and beverage company. This included complying with hygiene protocols, wearing appropriate protective gear, and ensuring that all safety measures were in place to maintain the highest standards of cleanliness and safety throughout the project
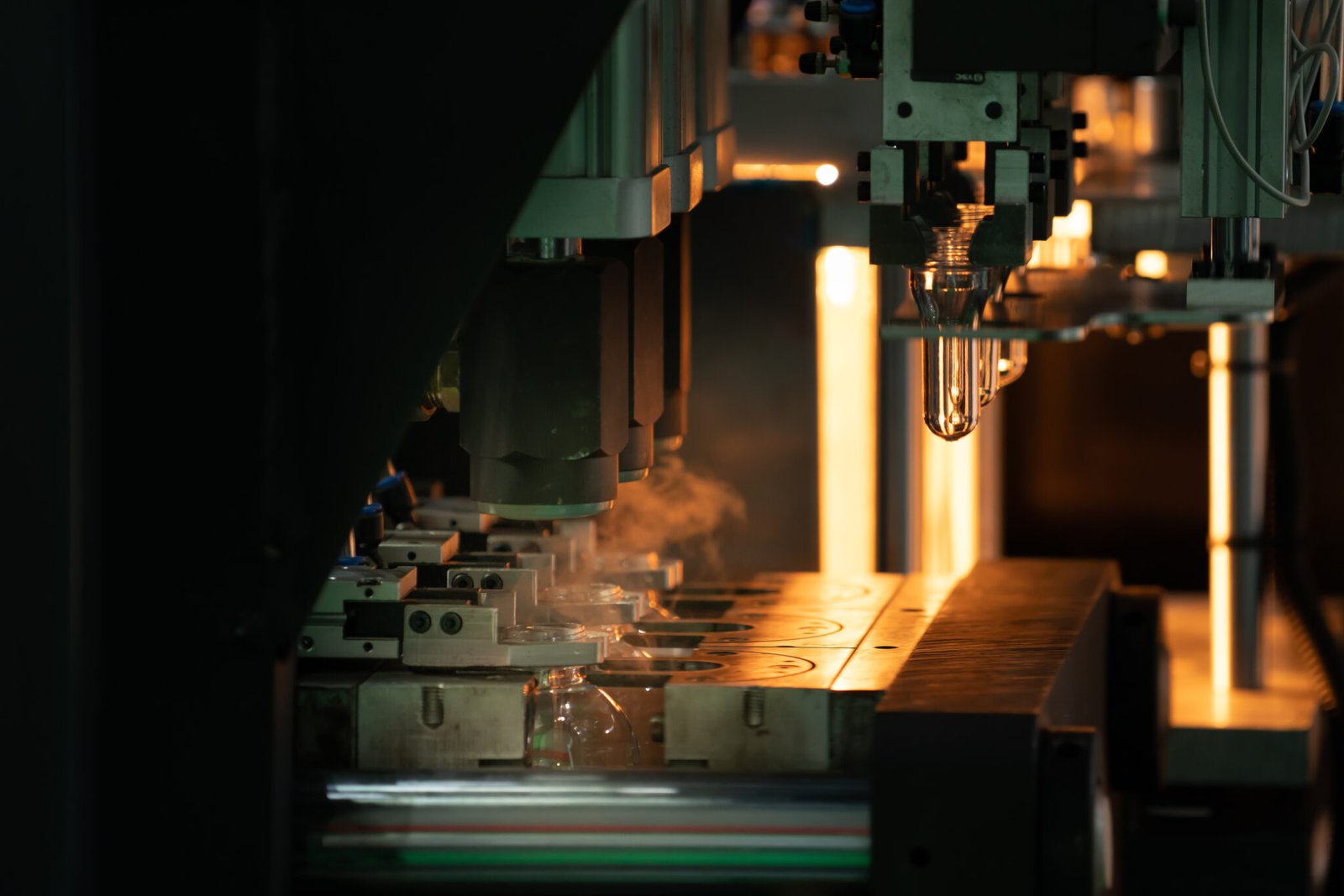
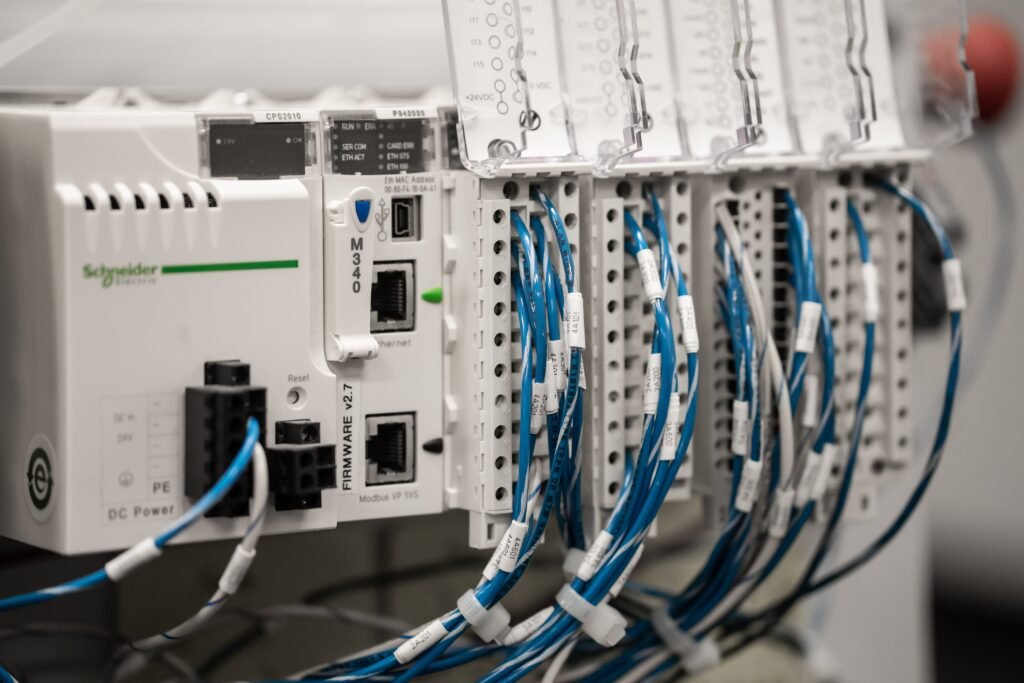
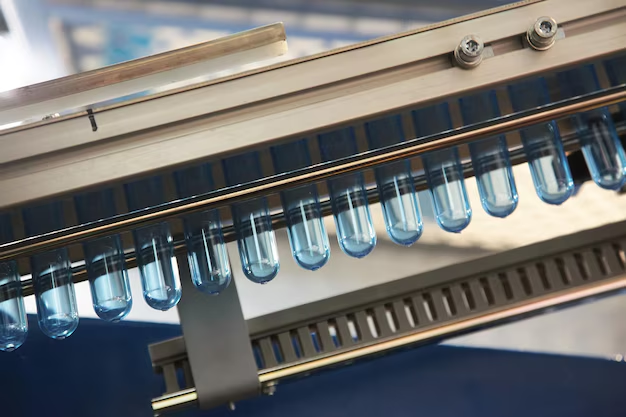
Project Summary :
- Conducted an onsite meeting with the client’s Maintenance team during the initial stage.
- Reviewed project data and designed a customized automation solution.
- Designed and developed the control panel within 15 days.
- Completed installation and commissioning within the scheduled 7-day shutdown period.
- Control panel included Schneider M340 Series PLC and GXU Series HMI.
- PID loops were precisely tuned for accurate barrel temperature control.
- System included key interlocks, access-level restrictions for safety, and integrated historical trends and alarm logs.
- Thorough testing and commissioning were completed.
- Delivered with detailed training and full documentation.
- Achieved 100% customer satisfaction.