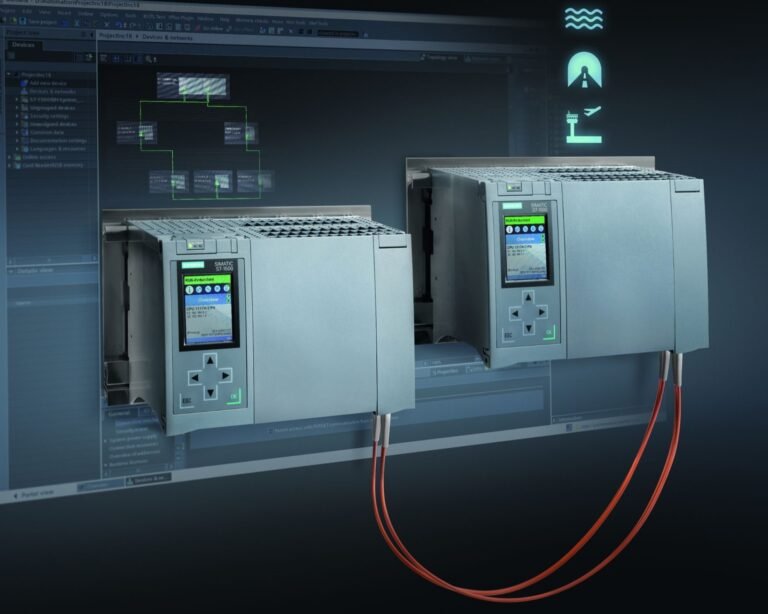
Control and monitor your operational processes
Powered by Siemens, the Compact PLC Series SIMATIC S7-1200 is best suitable for mid-range industrial applications. With its high-speed processing, it helps the control panel to execute tasks faster. It supports IEC 61131-3 programming languages to provide the utmost flexibility. PLC model supports all major communication protocols like Profinet, Profibus, Modbus, Ethernet etc.
Enhance productivity with high-end automation and efficiency
The Siemens SIMATIC S7-1500 controller is one of the latest PLC models for control panels. Equipped with advanced technologies, it ensures that your machinery performs with excellence. This model allows for high-end customization with various I/O modules. In addition to this, it detects faults and provides real-time system updates to avoid last-minute contingencies.
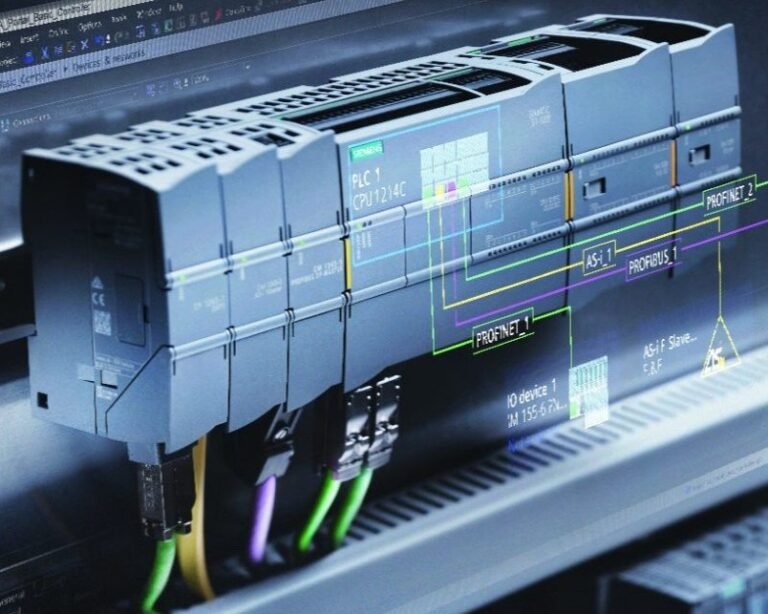
Modules for all prominent PLC Series

S7 1200
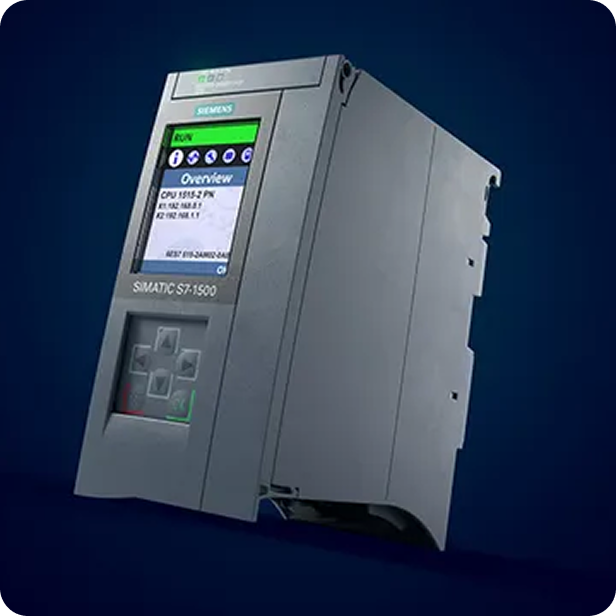
S7 1500
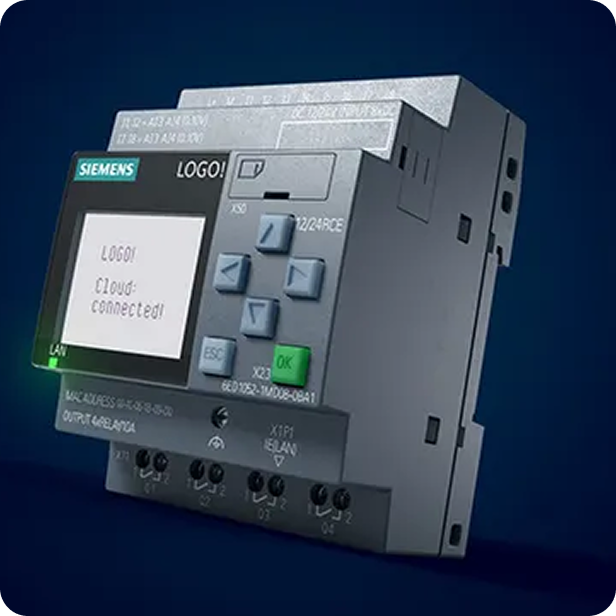
LOGO
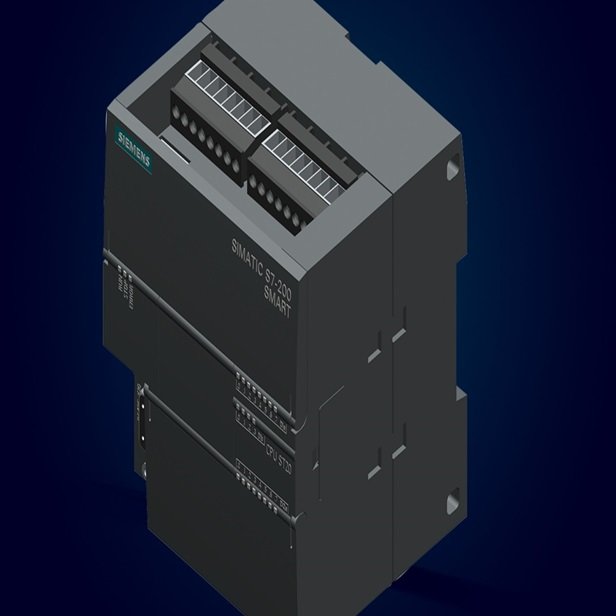
S7 200 SMART
How PLC Control is
shaping different industries
Pharmaceutical
Optimizing Tablet Production
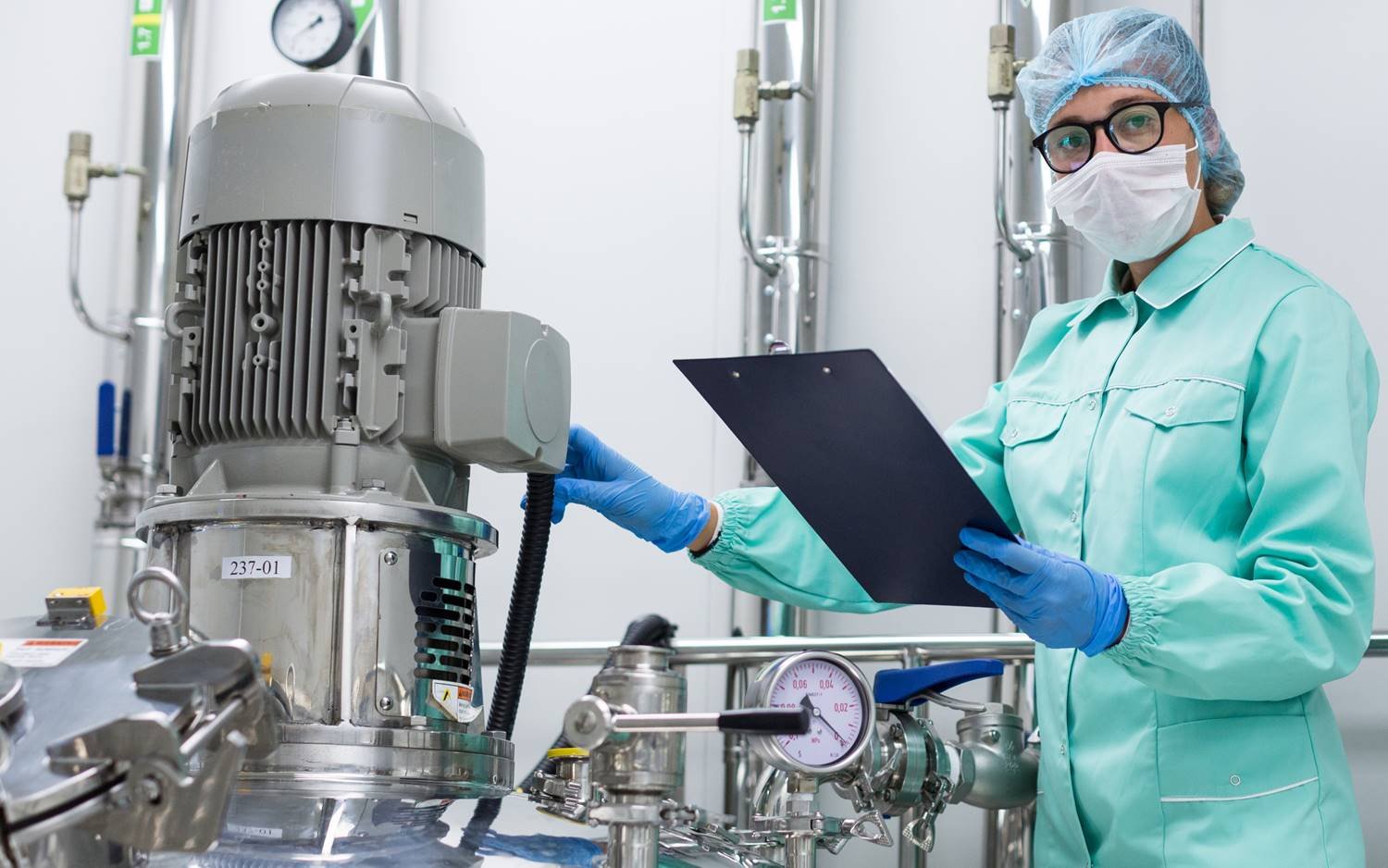
Programmable Logic Controllers (PLCs) are playing a significant role in shaping the pharmaceutical industry, particularly in the area of automated manufacturing processes. One key application is the tablet production process. In tablet manufacturing, PLCs are used to control and monitor various stages of the production process, including:
Blending | Granulation | Compression and coating | Packaging
PLCs provide high precision, reliability, and compliance with regulatory standards (like GMP), ensuring that tablet production is
consistent, safe and traceable. This automation minimizes human error, reduces waste and boosts production efficiency which is essential for meeting the pharmaceutical industry’s stringent quality standards.
Food & Beverage
Automated Bottling & Packaging
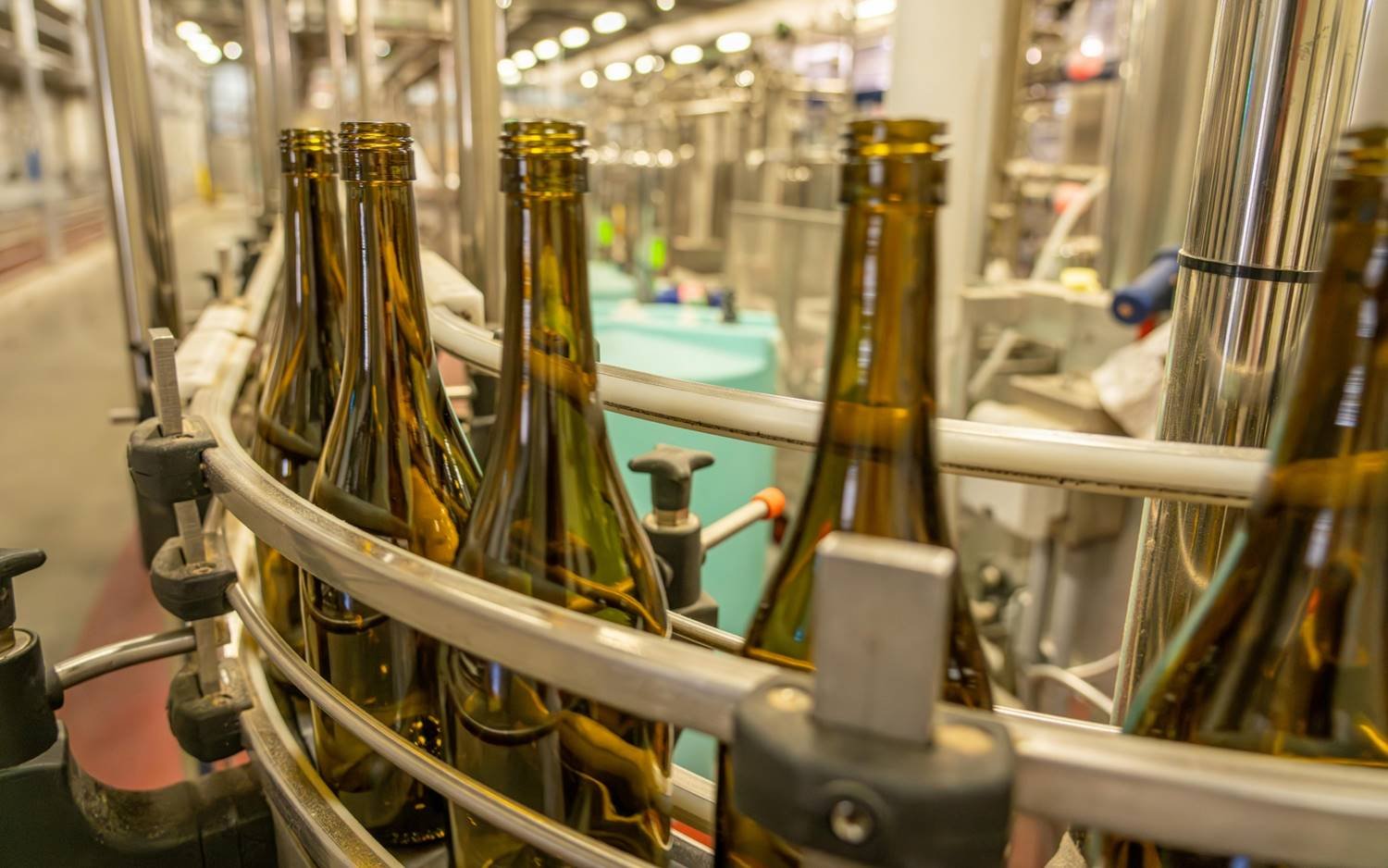
PLCs are transforming the Food & Beverage industry by automating critical processes, leading to higher efficiency, better quality control and reduced operational costs. One prominent application of PLCs in this industry is automated bottling and packaging lines. Bottling and packaging are critical steps where speed, accuracy and consistency are essential. PLCs control various parts of the bottling process, such as:
Filling | Capping | Labeling | packaging
They offer precise control over these operations, ensuring that each product is filled to the correct level, sealed tightly and labeled properly without human intervention.
Oil & Gas
Remote Pipeline Monitoring & Control
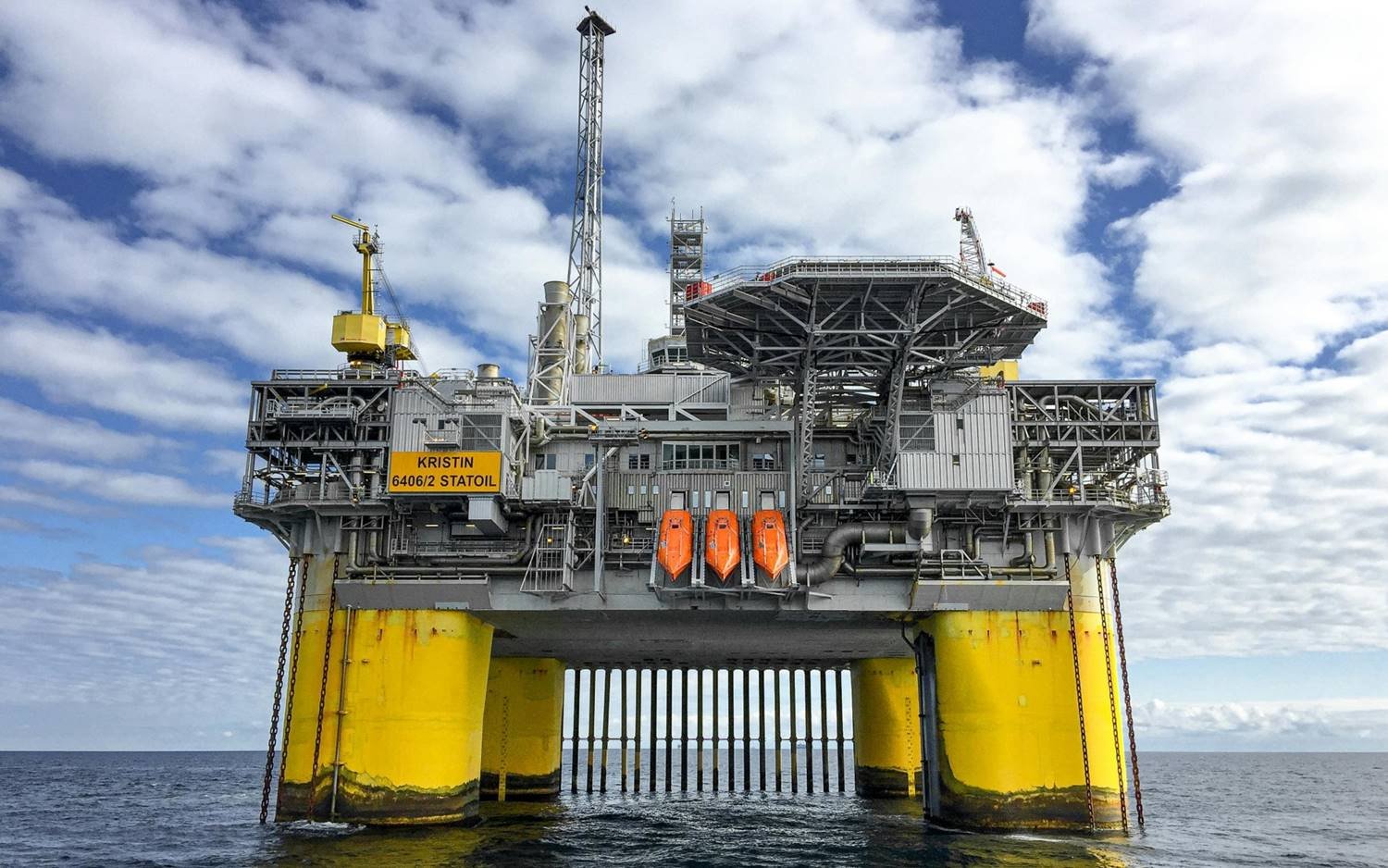
PLCs are playing a crucial role in the Oil & Gas industry by helping enhancing efficiency and improving safety. One of the most important applications of PLCs in this sector is in remote pipeline monitoring and control. In the case of a pipeline leak, the PLC system can quickly detect unusual pressure drops or changes in flow rates, activate safety measures like closing valves or diverting the flow and send alerts to operators. This reduces the risk of catastrophic events, such as oil spills or explosions and ensures regulatory compliance.
PLCs have a direct impact on operational cost reduction, risk mitigation and environmental protection, all of which are critical in the highly regulated and safety sensitive Oil & Gas industry.
Paint & Coatings
Automated Mixing and Blending
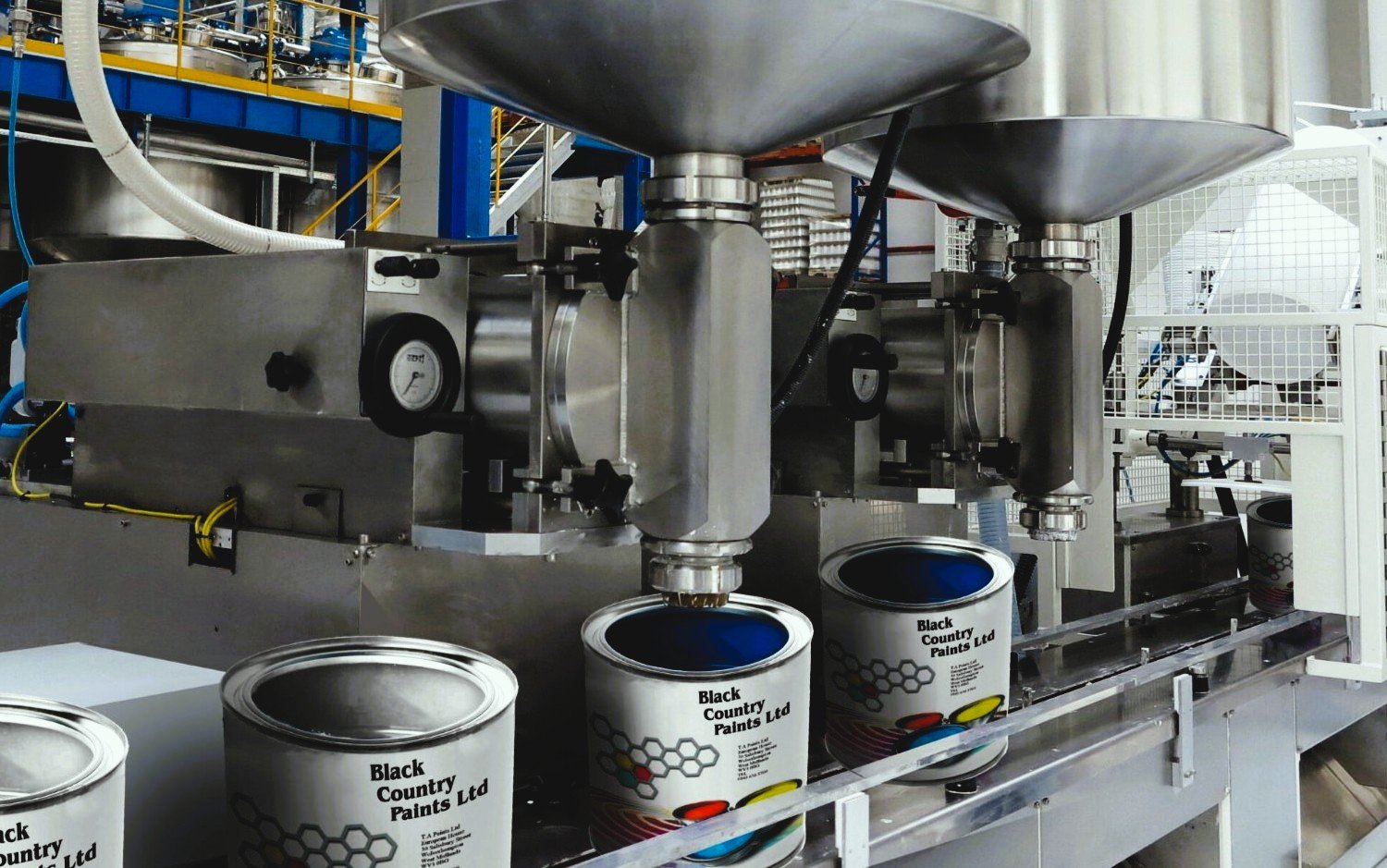
In the Paint & Coatings industry, PLCs are significantly improving production efficiency, product consistency and overall quality control. One of the most important applications of PLCs in this industry is automated mixing and blending of paint formulations. PLCs control and automate the mixing of raw materials such as pigments, solvents, resins and additives, to create paint formulations with precise and consistent properties. In large-scale paint manufacturing, this automation leads to improved product quality, as each batch is made with precise control over ingredients and conditions. It also speeds up production, reduces manual labor and enhances safety by minimizing the need for direct human intervention in potentially hazardous areas, like handling solvents and chemicals.
PLC & RIO Modules
-
Pharma Industry
-
F&B Industry
-
Oil & Gas Industry
-
Paint Industry
Optimizing Tablet Manufacturing Process
Programmable Logic Controllers (PLCs) are playing a significant role in shaping the pharmaceutical industry, particularly in the area of automated manufacturing processes. One key application is the tablet production process.
In tablet manufacturing, PLCs are used to control and monitor various stages of the production process, including:
Blending of ingredients: Controlling the speed and duration of mixing, ensuring that the active pharmaceutical ingredients (APIs) and excipients are blended uniformly.
Granulation: Maintaining the required moisture content, speed, and pressure during granulation, this is crucial for the quality of the tablets.
Tablet compression and coating: Regulating the compression force during tablet pressing and ensuring the tablet coating process is consistent.
Packaging: Automating the packaging line, including the filling, labeling, and sealing processes, to maintain efficiency and accuracy.
PLCs provide high precision, reliability, and compliance with regulatory standards (like GMP), ensuring that tablet production is consistent, safe and traceable. This automation minimizes human error, reduces waste and boosts production efficiency which is essential for meeting the pharmaceutical industry’s stringent quality standards.
PLCs have revolutionized pharmaceutical manufacturing by enabling more precise control over the entire tablet production process, leading to higher quality products and improved operational efficiency.
Taking advantage of two simulation environments
Magneti Marelli chose to develop its controls strategy with Simulink while using Simcenter Amesim to model the multidomain engine components. The two solvers are in communication, and inputs and outputs are exchanged between the two environments. The creation of a complete virtual system environment enables simulation of the system behavior, for both hydraulic components and software. Simcenter Amesim and Simulink work together to improve the reliability of the controls strategy.
“We were able to match the advantages of these two environments to build complete model-based software including a multidomain system built using Simcenter Amesim and controls model built using Simulink. It enables us to optimize the product and components design from the first stages,” says Paolino.
Taking advantage of two simulation environments
Magneti Marelli chose to develop its controls strategy with Simulink while using Simcenter Amesim to model the multidomain engine components. The two solvers are in communication, and inputs and outputs are exchanged between the two environments. The creation of a complete virtual system environment enables simulation of the system behavior, for both hydraulic components and software. Simcenter Amesim and Simulink work together to improve the reliability of the controls strategy.
“We were able to match the advantages of these two environments to build complete model-based software including a multidomain system built using Simcenter Amesim and controls model built using Simulink. It enables us to optimize the product and components design from the first stages,” says Paolino.
Taking advantage of two simulation environments
Magneti Marelli chose to develop its controls strategy with Simulink while using Simcenter Amesim to model the multidomain engine components. The two solvers are in communication, and inputs and outputs are exchanged between the two environments. The creation of a complete virtual system environment enables simulation of the system behavior, for both hydraulic components and software. Simcenter Amesim and Simulink work together to improve the reliability of the controls strategy.
“We were able to match the advantages of these two environments to build complete model-based software including a multidomain system built using Simcenter Amesim and controls model built using Simulink. It enables us to optimize the product and components design from the first stages,” says Paolino.
Related Products
Explore more products
Specially Crafted Services
Experience-driven services, crafted to align with your requirements.
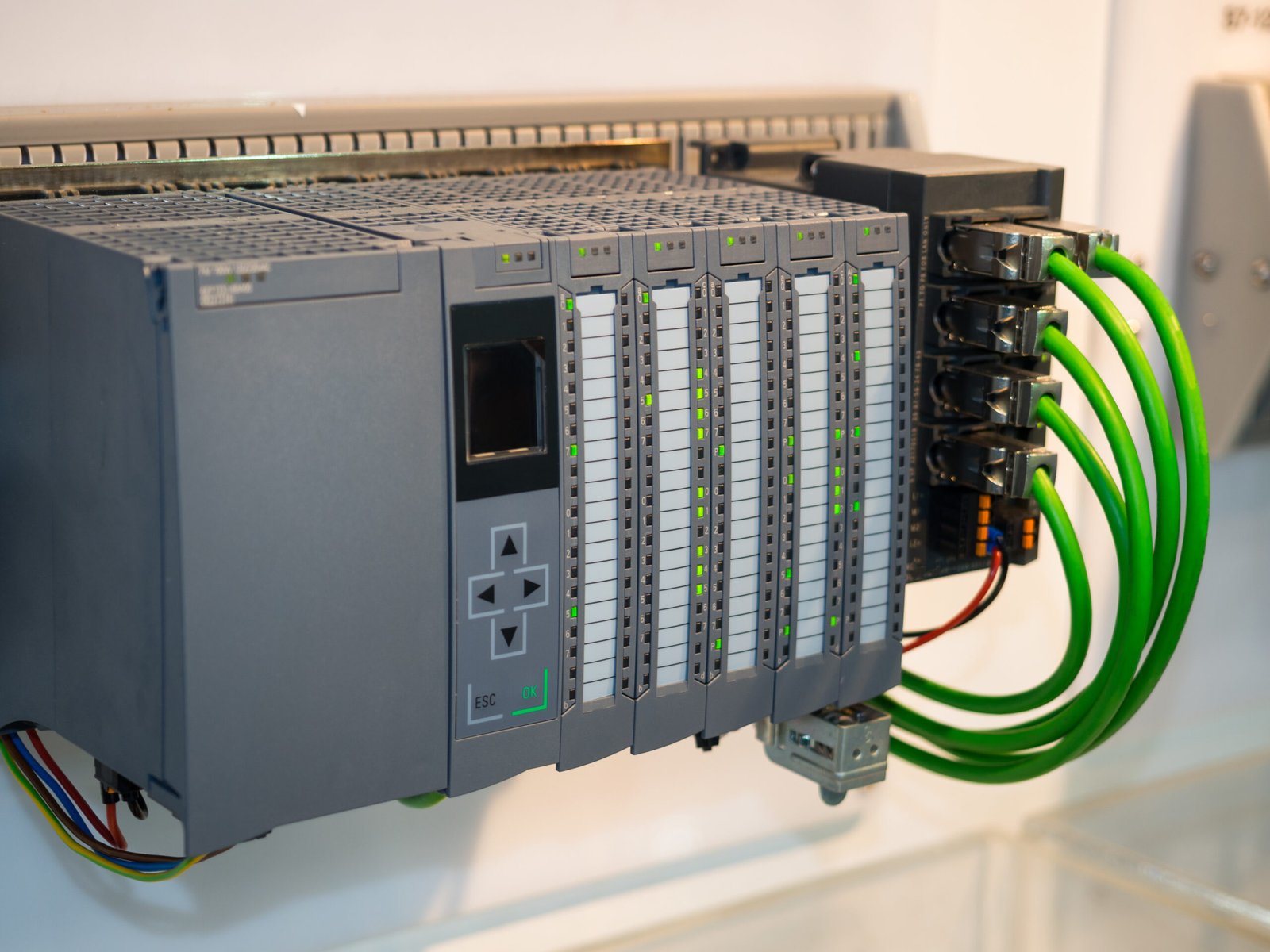
PLC Migration and Upgrade Services
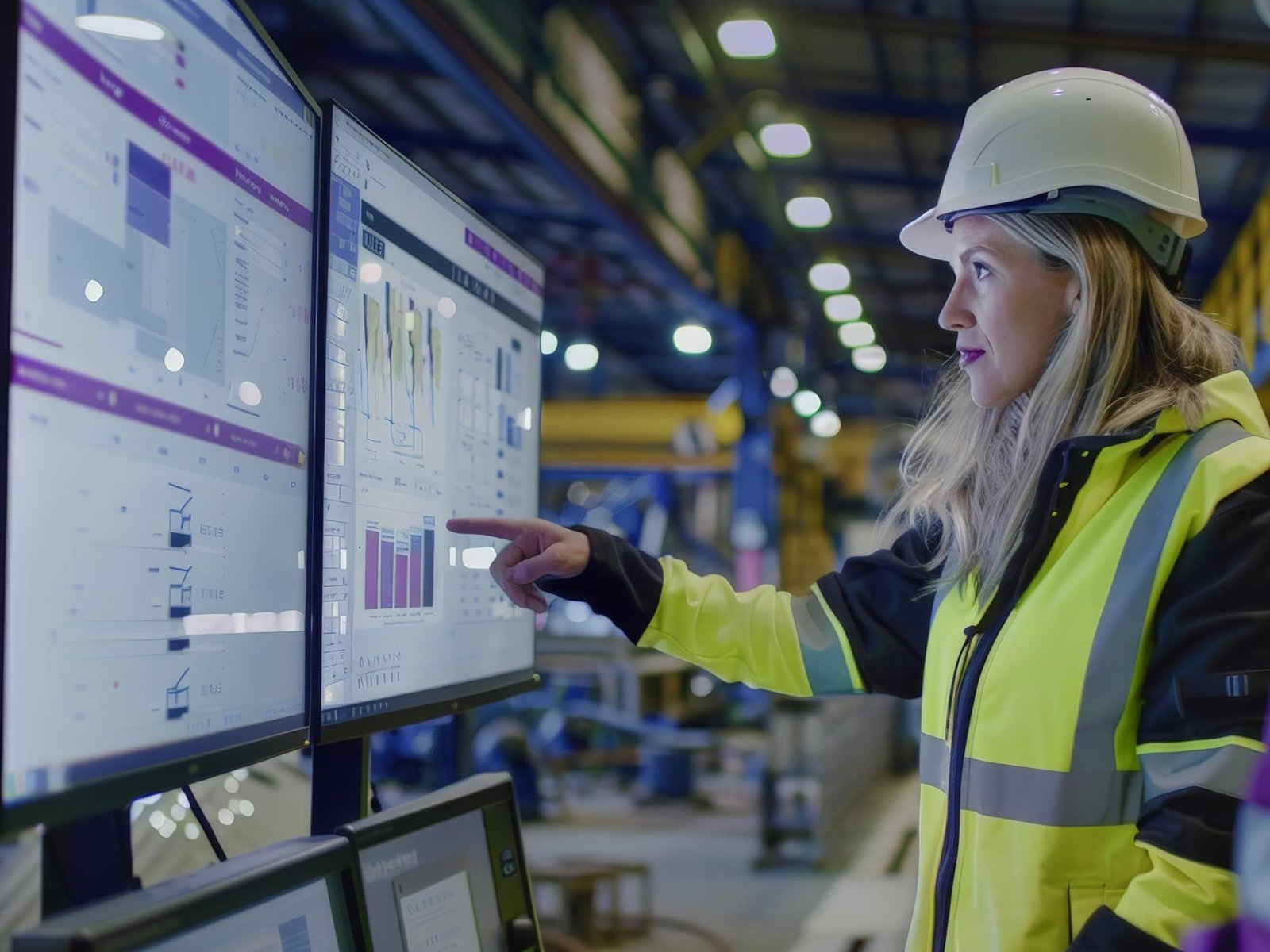
Energy Monitoring Solutions
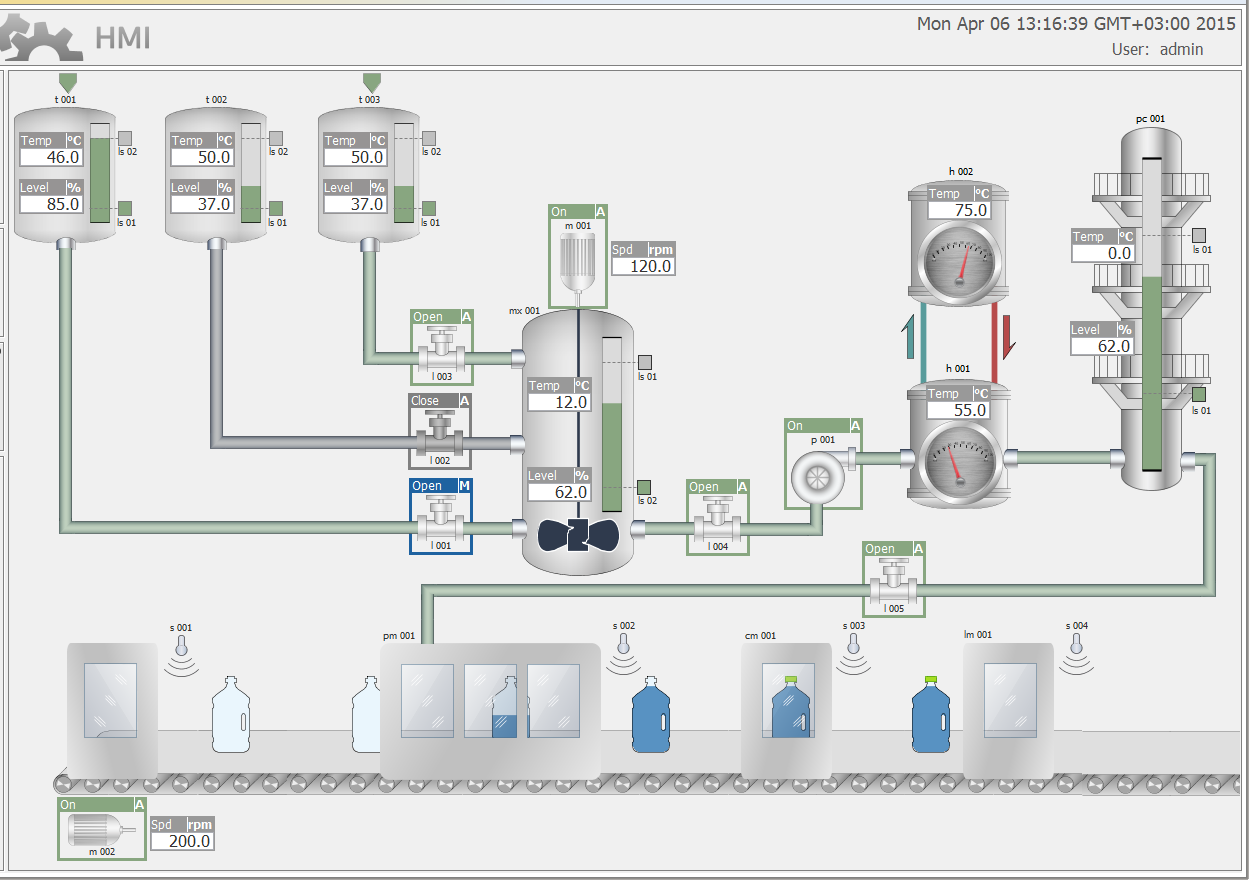
UX UI Designing for HMI & Scada Screens
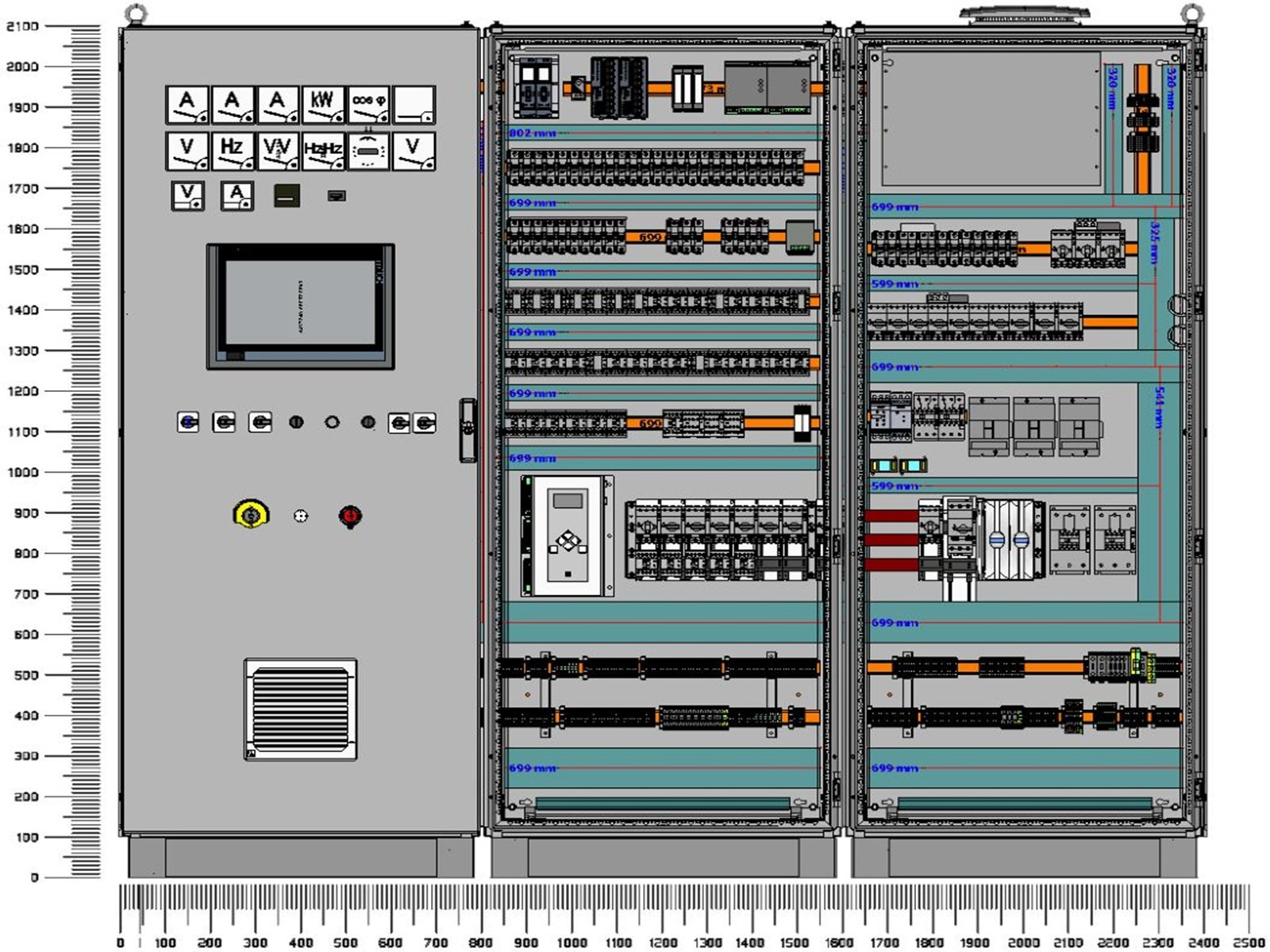